Оцени сайт
Как выжигать Dental Cast и Dental Cast Cherry PRO?
Введение
HARZ Labs Dental Cast Cherry и Dental Cast Cherry PRO – выжигаемые материалы, позволяющие получать великолепные результаты как при литье коронок, мостовидных конструкций, так и при прессовке Emax. Правильная моделировка, соблюдение режимов постобработки и отжига обеспечат вам стабильный и высококачественный результат.
Моделирование каркасов
Первым этапом является моделирование каркасов, сделать это можно в специальных программах, таких как Exocad, 3Shape и т.д.
На что нужно обратить внимание при моделировании?
- Протяженность конструкции.
- Параллельность поточенных культей.
- Качество проточки культи.
- Толщина каркаса.
- С какого сканера получен stl файл (с интраорального или лабораторного).
Все это будет влиять на выставление цементного зазора. В качестве примера разберем данный клинический случай: На данной работе нужно отмоделировать и изготовить каркас на 14 единиц на 7 культях.
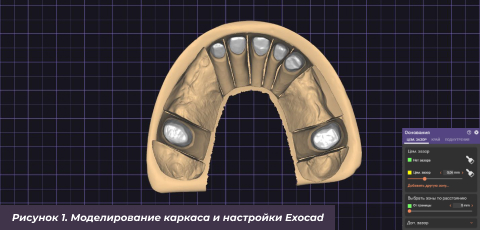
Параметры меняются в зависимости от опыта техника, калибровки принтера, предпочтения врача или самого техника. Поэтому указанные параметры подходят конкретно к данному случаю и могут отличаться по списку причин, указанных выше. На величину цементного зазора влияет также точность принтера и правильный подбор режимов печати. Для начала работы и печати первых каркасов и коронок рекомендуется выставить зазор порядка 0,08-0,1 мм а при необходимости этот зазор уменьшить.
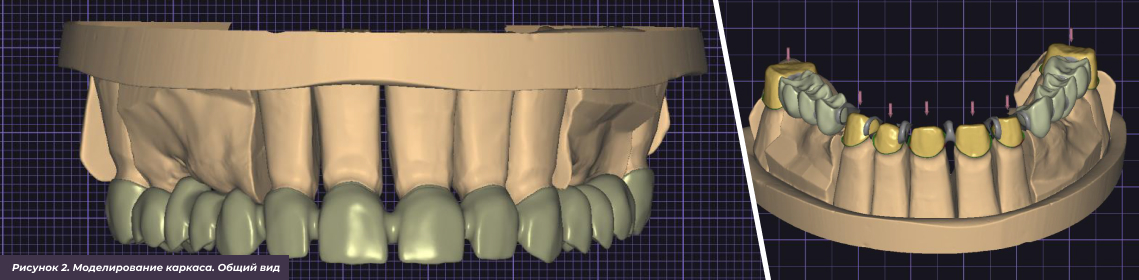
Печать
Перед запуском файла на печать требуется подобрать оптимальные параметры печати. Сделать это можно, используя калибровочный тест HARZ Labs. Отправные настройки вы можете найти на нашем сайте
Полученную модель отправляем в слайсер и выставляем поддержки. Поддержки должны удерживать модель на столике и устанавливаться во все минимальные точки, откуда идет построение модели. Также задача поддержек – удержать модель от раскачивания в процессе печати.
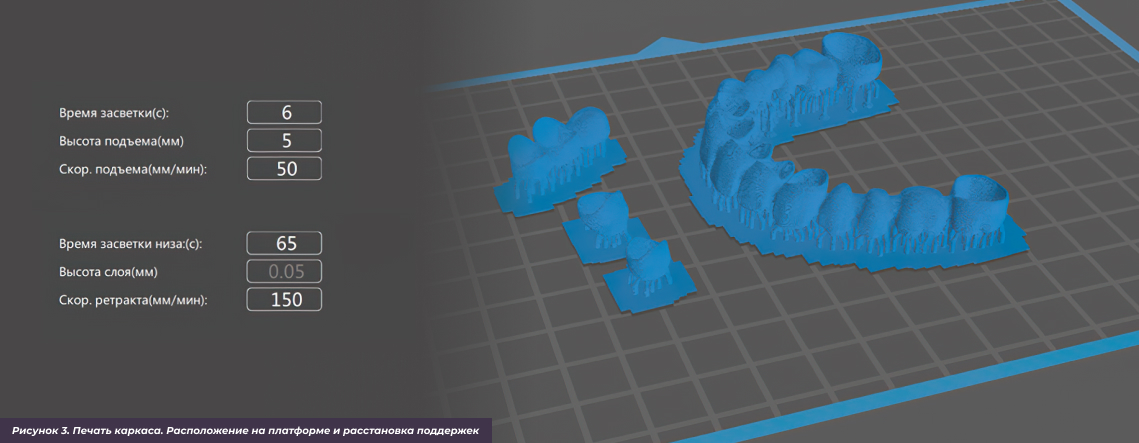
Параметры печати подобраны по результатам печати калибровочного теста. Печать происходила на настольном фотополимерном LCD принтере Elegoo Saturn.
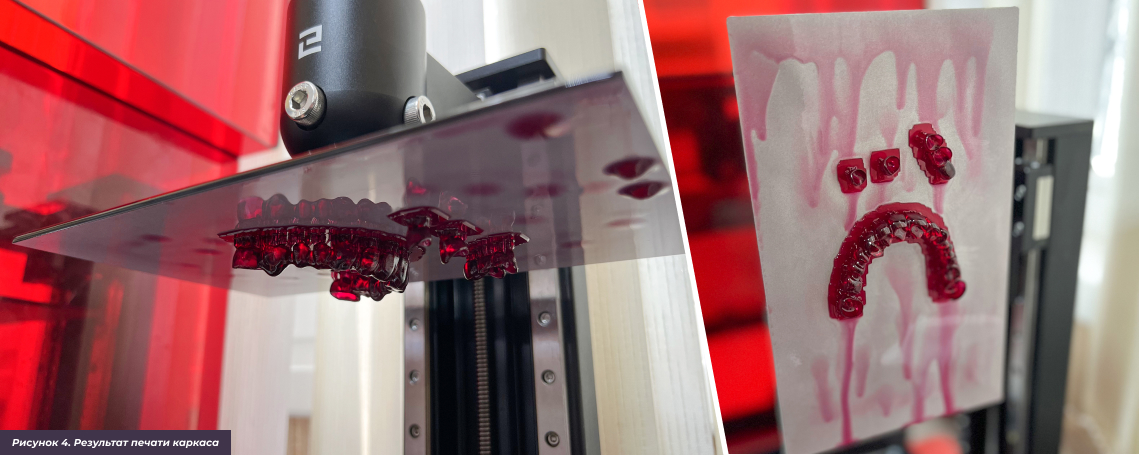
Постобработка
Важно соблюсти правильную постобработку для получения стабильного результата. Общие рекомендации по постобработке можно найти на сайте HARZ Labs в разделе техническая поддержка.
Какая постобработка требуется?
Данная работа обрабатывалась следующим образом.
- Снятие детали с платформы принтера.
- Первичная промывка в грязном спирте в течение 5 минут
- Финишная промывка с использованием ультразвуковой ванны в течение 5 мин.
- Продувка сжатым воздухом
- Прогрев в сухожаровом шкафу в течение 10 минут при температуре 50 градусов
- Дозасветка в УФ-камере
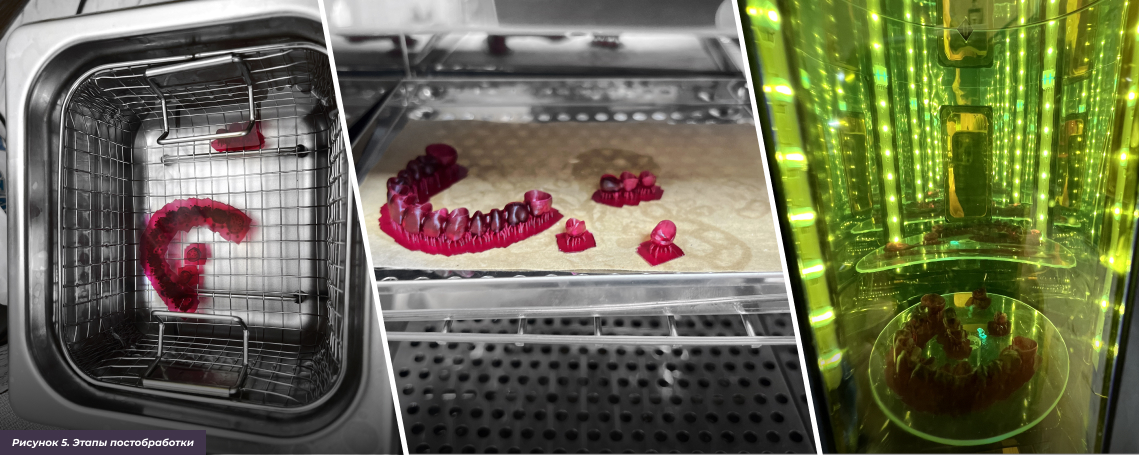
Примерка моделей
После проведения постобработки необходимо снять поддержки и примерить каркас на модель. Необходимо получить хорошее прилегание и отсутствие баланса.
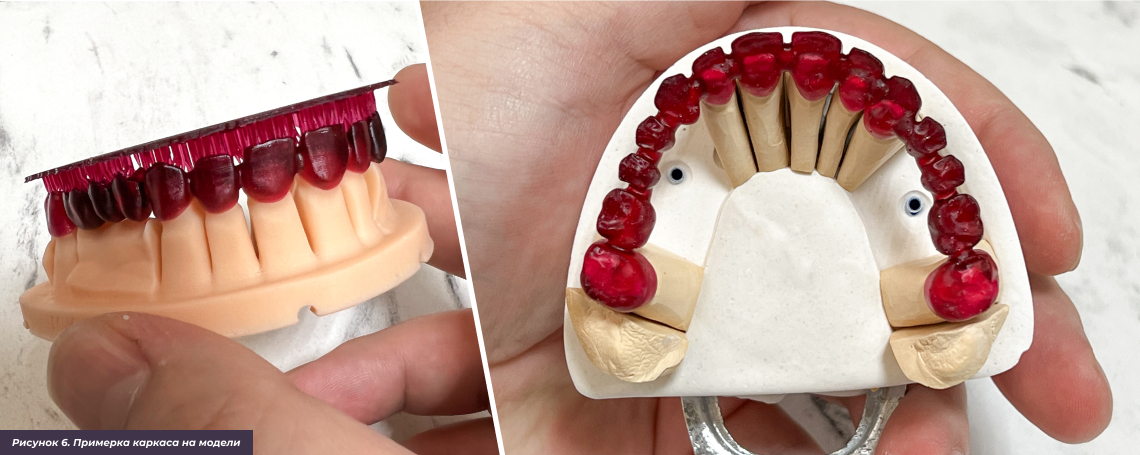
Создание литников и воздухоотводов
После печати и постобработки изделий необходимо создать правильную систему литников. Для их создания можно использовать обычный литейный воск, он имеет хорошую адгезию к отпечатанным моделям и продается уже калиброванным под нужную толщину. Расстановка литников зависит от объема, массы и протяженности конструкции. Завершив пайку литников, рекомендуется воспользоваться жидкостью для снятия напряжений с воска. Для снятия внутренних напряжений, использовалась жидкость Bego Aurofilm.
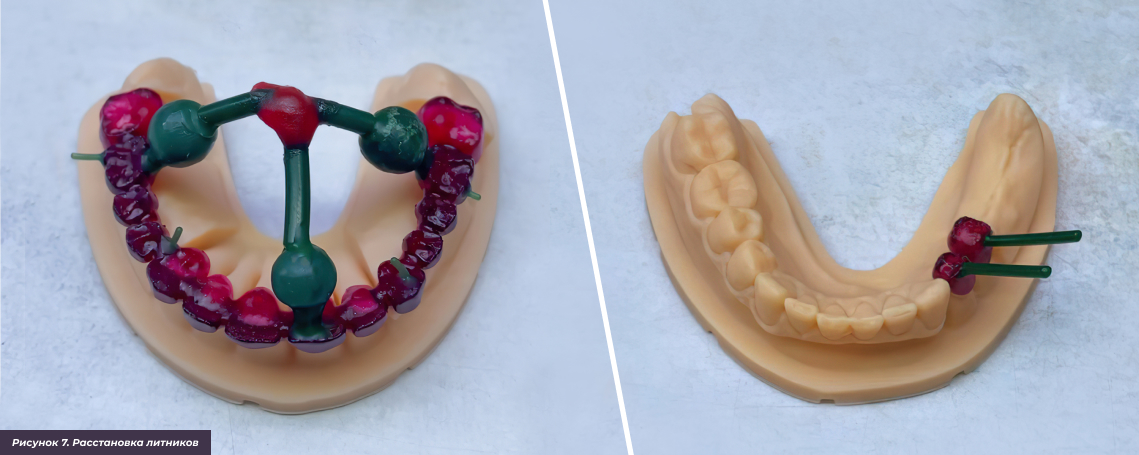
Подготовка формовочной массы
Следующим шагом является подготовка формовочной массы. В данном случае использовалась паковочная масса Bredent. Для отливки бюгелей можно использовать паковочную массу Bego Wirofine. Также можно использовать паковочные массы других производителей, но главное работать по инструкции производителя паковочной массы. Минимальное расстояние от края модели до стенок опоки должно быть не менее 5 мм. Для укрепления паковочной массы рекомендуется добавить 0,2% борной кислоты в общее замешивание и армировать металлической сеткой. Рекомендуется ставить воздухоотводы при отливке массивных конструкций. Концентрация смеси подбирается строго согласно инструкции производителя массы, после добавления жидкости рекомендуется перемешать массу вручную, а лишь затем помещать в вакуумный смеситель. Необходимо это для того, чтобы сухая смесь не была втянута вакуумным насосом до того, как начнется замешивание.

Заливка массы в форму
Заливать массу необходимо тонкой струей на вибростоле, что позволит заполнить форму максимально равномерно и без пузырей.
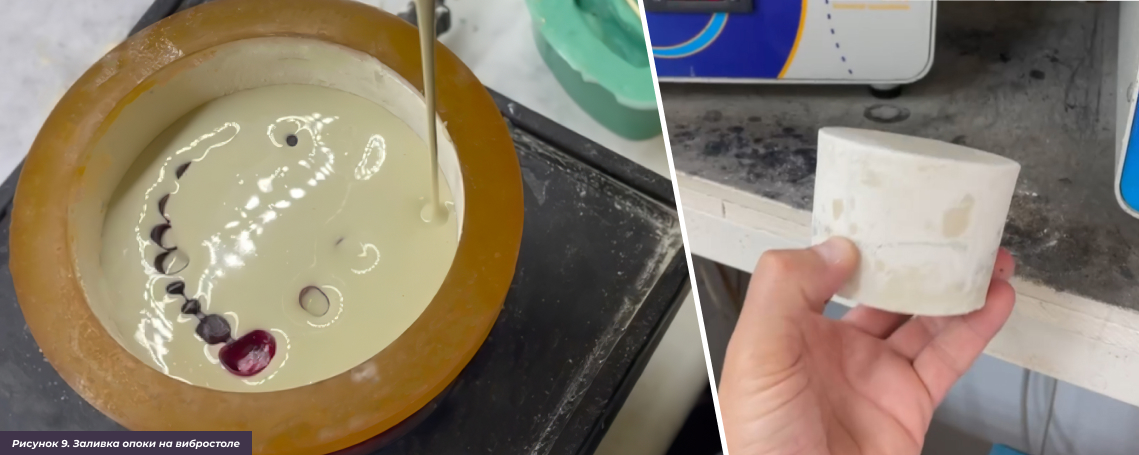
По окончании заливки необходимо дать массе затвердеть, а затем поместить опоку в холодную печь.
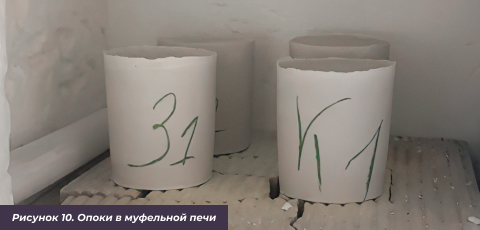
Прокалка опоки
Печь можно разогревать на максимально возможной скорости до 950 градусов и выдерживать время, рекомендованное производителем массы, но не менее 50 минут. Важно отметить, что на время выдержки влияет и количество опок в печи. Например, для одной опоки весом 100 гр достаточно 50 минут, а для 4-х необходимо уже 2 часа выдержки. При большом объеме работ можно использовать 2 муфеля и разделять прогрев на 2 этапа. Первичный прогрев опоки может осуществляться в первом муфеле при температуре 500 градусов порядка 15 минут, а второй этап прогрева проходит во втором муфеле при температуре 950 градусов.
Литьё
Следующим этапом является подготовка к литью.
- При литье каркасов использовался металл Shefner Ni-Cr.
- При литье бюгелей использовался металл Bego Wironit extra-hard.
Перед заливкой металла рекомендуется продуть опоку сжатым воздухом.
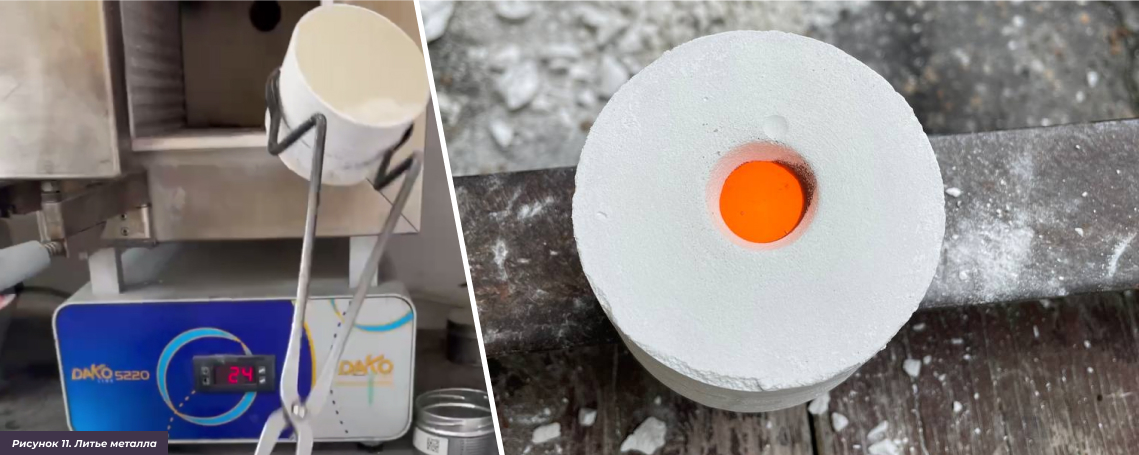
Извлечение и обработка модели
Для извлечения отлитой конструкции из опоки используется малое долото или легкий молоточек. Для ускорения этой процедуры может использоваться пневмодолото для распаковки опок. Прочно приставшая к поверхности отливки паковочная масса и оксидный слой удаляются вручную или автоматически. Дополнительно используется специальный песок с размером зерна 250 микрон под рабочим давлением 4-6 атмосфер (вручную) или 5-6 атмосфер (в автоматическом режиме). Специальным автоматическим пескоструйным аппаратом с высоким давлением достигается абсолютно чистая поверхность конструкции.
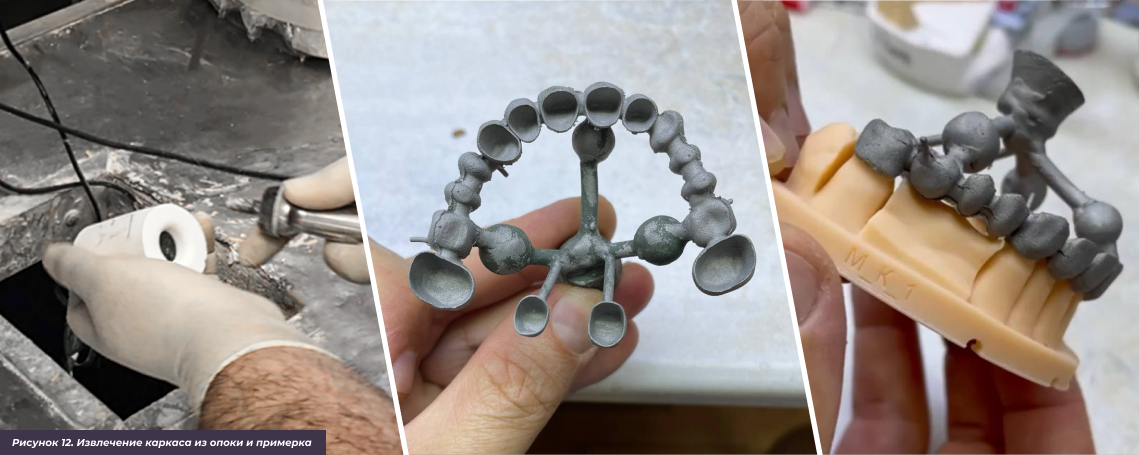
Результат
Конечный результат примеряется на мастер модели, проверяется посадка и оценивается качество поверхности литой детали.
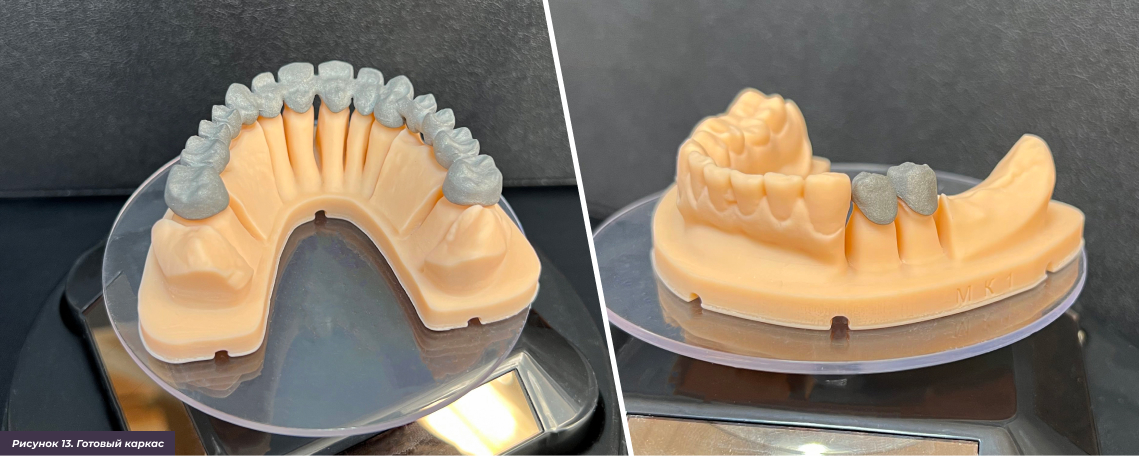
Правильное соблюдение технологии позволяет получить высокое качество отливок и максимально точные размеры без дополнительной ручной обработки изделий.
За предоставленную информацию благодарим Арсения Фёдорова и Юрия Абрамова.